
Kooperation
Modelwise und innotec
Kooperation bei der Innovation der Funktionalen Sicherheit
Modelwise, ein Spin-off der Technischen Universität München, das Software für automatisierte Analysen der Funktionalen Sicherheit entwickelt, und innotec GmbH, ein auf Funktionale Sicherheit spezialisiertes Beratungsunternehmen und seit 2020 Teil der TÜV AUSTRIA Group, gaben ihre strategische Partnerschaft zur Innovation der Funktionaler Sicherheit bekannt. Die Zusammenarbeit kombiniert das innovative Software-Tool von Modelwise Paitron, anwendbar für alle (A)SILs gemäß IEC 61508 und ISO 26262, und innotec’s Expertise in Funktionale Sicherheit einschließlich HARA, Sicherheitsanforderungsmanagement und sicherer Hardware- und Softwareentwicklung.

TRUSTED AI by TÜV AUSTRIA
SmartScan-Technologie von SCANTEC:
Funktionale Vertrauenswürdigkeit durch “TRUSTED AI”-Zertifizierung bestätigt
Die SmartScan-Technologie zur Abfallentsorgung von SCANTEC, einer Tochtergesellschaft von ZOELLER, wurde kürzlich vom TÜV AUSTRIA mit dem Prüfzeichen “TRUSTED AI Application” für ihre funktionale Vertrauenswürdigkeit zertifiziert.

TÜV AUSTRIA AUTOMOTIVE
Sicher unterwegs im Sommer:
Tipps für eine entspannte Urlaubsfahrt
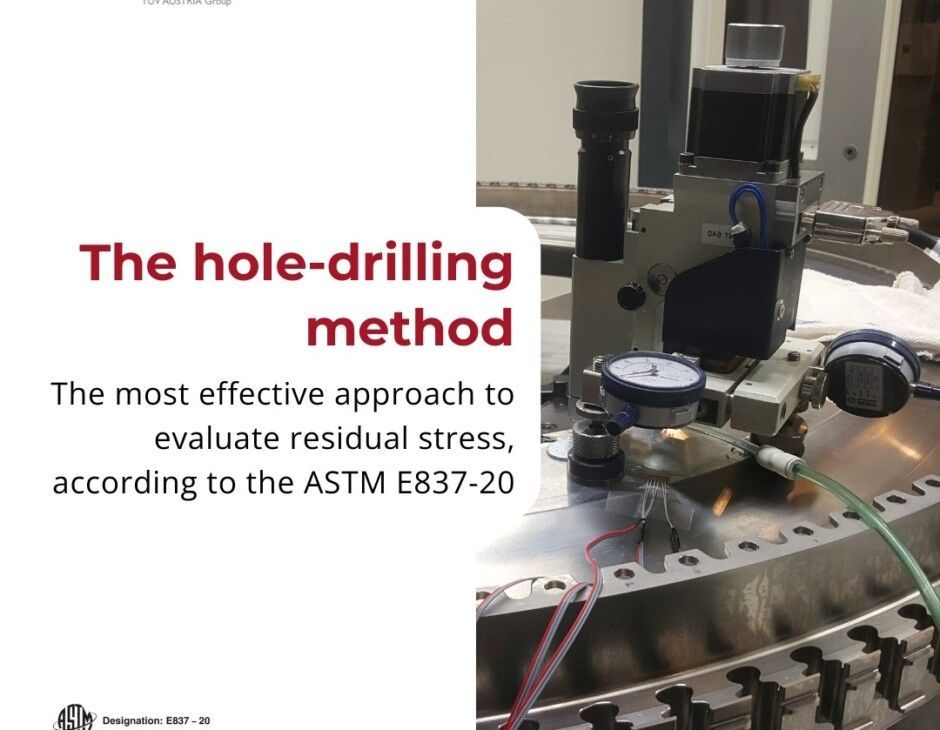
Messtechnik
SINT Technology: Bohrlochmethode
Zerstörungsfreies mechanisches Verfahren zur Messung von Eigenspannungen
SINT Technology, ein Unternehmen der TÜV AUSTRIA Group, führt Überprüfungen des Eigenspannungsniveaus in mechanischen Komponenten mittels der Bohrlochmethode durch.

Expertentag
20. Juni 2024:
TÜV AUSTRIA Medizinprodukte-Tag 2024
Am 20. Juni 2024 findet der alljährliche TÜV AUSTRIA Medizinprodukte-Tag in Kooperation mit mdc medical device certification GmbH statt.

Golfen für einen guten Zweck
TÜV AUSTRIA Golf Charity Turnier
14. Juni 2024
TÜV AUSTRIA veranstaltet ein Golf Charity Turnier am Freitag, 14. Juni 2024 zu Gunsten des Schulprojekts Bethel High School in Nanoro im westafrikanischen Burkina Faso.



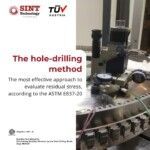


Unser
TÜV AUSTRIA Showcase
Unsere Lösungen der Woche
-
Umweltsimulation
Branche: Industrie
-
ICT Industrielle Computertomographie
Branche: Industrie
-
Ankaufs- und Verkaufstest für Einfamilienhäuser und Gewerbeimmobilien
Branche: Bau & Real Estate
Unterstützung benötigt?
tami ist der digitaler Wegbereiter und hilft unseren Kund:innen bei ihren Anliegen.
tami ist der TÜV AUSTRIA Wegbereiter für Unternehmen in der digitalisierten Marktlandschaft. In Österreich und auf der ganzen Welt – hosted in Austria. tami zeigt den richtigen Weg – auch bei der Suche auf unserer Website. Frag’ tami@tuv.at
´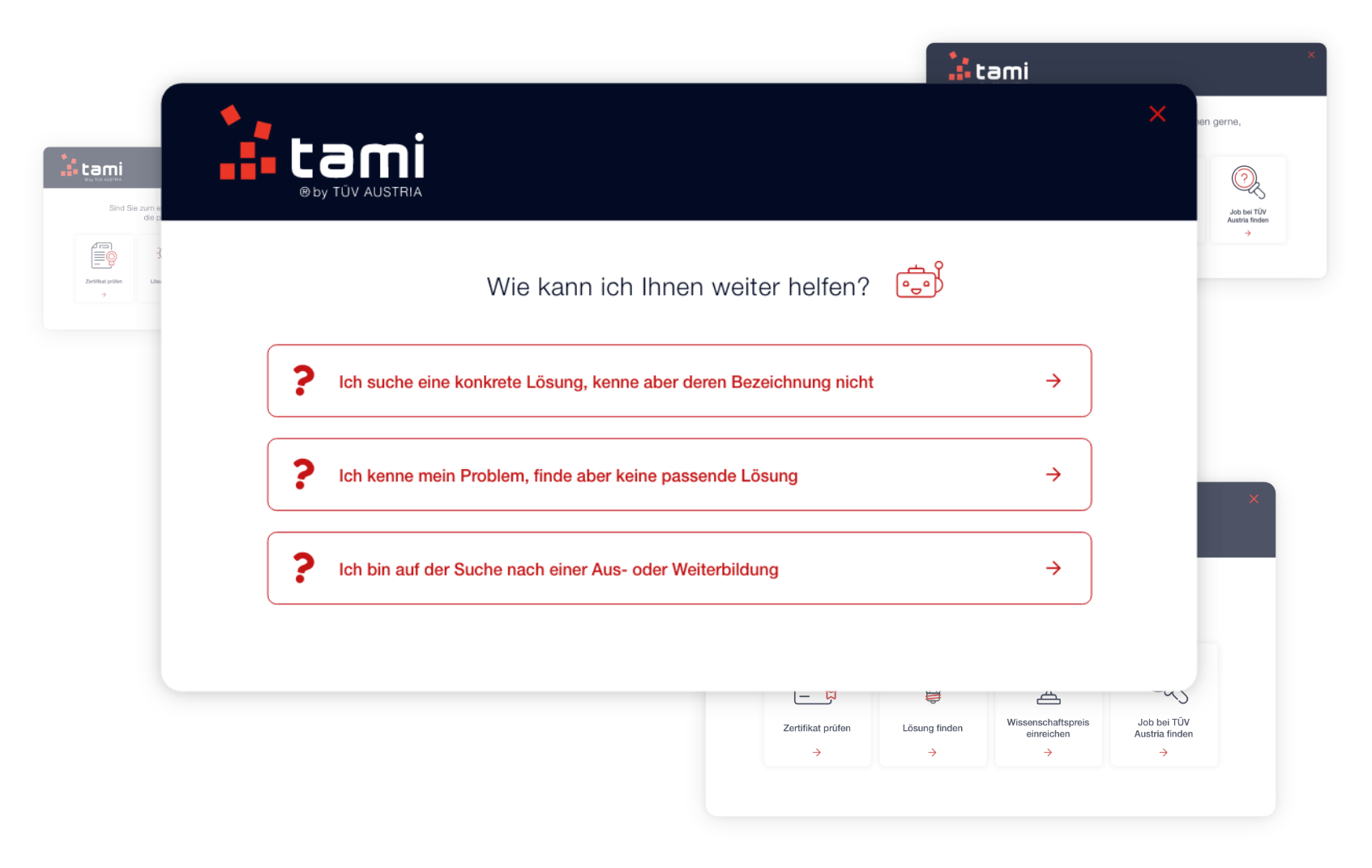
Unsere Leistungen
überzeugen
Mehr über unsere Lösungen erfahren -
Audit & Certification TÜV AUSTRIA zertifiziert Managementsysteme, Personen und Produkte.
Entdecken -
Fachverlag Der TÜV AUSTRIA Fachverlag bietet ein umfangreiches Sortiment an Fachbüchern, Skripten und Dokumentationshilfen.
Entdecken -
Guidance Die TÜV AUSTRIA Expert_innen begleiten Sie gerne rund um das Thema “Sicherheit”.
Entdecken -
Testing & Inspection TÜV AUSTRIA agiert als unabhängiges Prüf- und Inspektionsunternehmen.
Entdecken -
Training Die TÜV AUSTRIA Akademie bietet mehr als 2.400 praxisnahe Kurse für jedes Weiterbildungsziel.
Entdecken
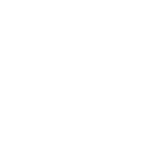
Gründe, warum Sie uns vertrauen können
-
1 %
höchst zufriedene Kund:innen
-
+ 1
System-, Personen- und Produktzertifizierungen
-
1
Sprachen werden bei TÜV AUSTRIA intern gesprochen
-
+ 1
Lösungen im Dienstleistungssektor bieten wir an